This GM alternator upgrade was preformed on a 1987 4Runner with the 22RE.
For other popular Toyota alternator upgrade info, please see notes below.
The factory alternator on my 1987 4Runner 22RE was rated at putting out 60-70amps. Not only was this woefully under-powered for the 4Runner's build, but this alternator had seen one too many mud holes and had decided to kick the bucket. I decided to upgrade to the CS-144, which is rated at 140amps, and is more appropriate for my power needs.
Side note: if your "Brake" and "Charge" lights come on at the same time, it's an indication of an alternator issue. You can have your alternator checked, while installed in the vehicle, at most auto part stores.
To begin the CS-144 alternator upgrade, you will need a few parts.
- CS-144 Alternator
- I went with the 1995 Cadillac Fleetwood alternator from O'Reilly's Auto Parts. When choosing your CS-144 for your 22RE, you want one with an internal regulator. The 1st generation of 4Runners had internal regulators, which makes wiring very simple. Details below.
- TrailGear GM-to-Toyota relocation bracket
- The CS-144 alternator is massive, and the factory bracket will not fit it. Some people try to get by with stacking washers on the bracket. This will not work with the CS-144. You need the extended adjustment bracket (top piece).
- V-belt pulley
- The CS-144 is only offered with a serpentine belt pulley. The v-belt pulley you need is a Delco 24-1100-1. Most auto repair shops can easily swap these pulleys for you. I used an alternator-specific shop for both my pulley purchase and install. It cost me $7 and 10-minutes of my time. Completely worth it.
- Extended V-belt
- You need a belt 1.5" longer than your factory belt. The belt I used was a MasterPro 7360, a 10mm-930mm belt.
- 3-wire GM connector
- O'Reilly's part number BWD PT200
- 78" 4-gauge wire. A battery cable works great here
- The factory alternator-to-battery cable is way too small for this upgrade.
- 4-gauge crimp-on eyelets
- Found near the battery cables at the parts store. I found mine at Auto Zone,
- 150amp circuit breaker or inline fuse
- A high-quality in-line fuse of this size can be expensive. I opted for the circuit breaker design so I can reset it if it blows. I also found this at Auto Zone, part number BP-CB185-150.
- 10mm, 12mm, and 14mm ratcheting box-end wrenches
- Because they will preserve whatever sanity you have left.
Side Note: You will be removing your entire external cooling system during this upgrade. New hoses and radiator would be a very easy repair at this point. New AC and power steering belts are recommended as well.
Now that you have your parts, you're ready to dive in and upgrade your alternator.
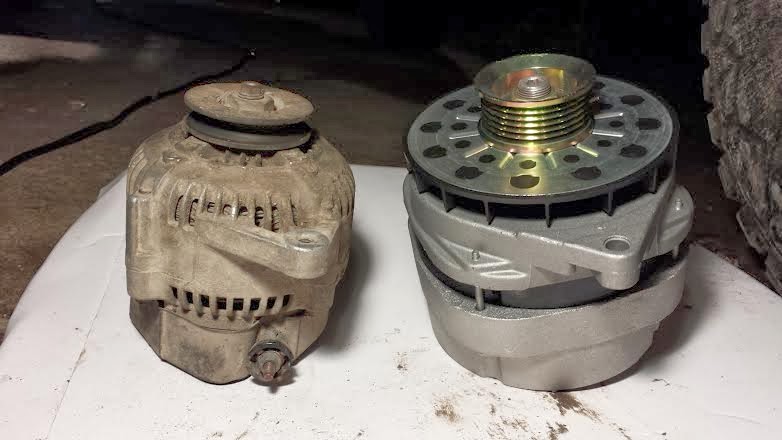 |
Factory alternator
vs.
1995 Cadilliac Fleetwod CS-144 |
To begin removing your factory alternator, unhook the negative battery terminal. Drain and remove lower radiator hose. Unplug the factory plug from the alternator, and unbolt/remove the bottom swivel alternator bolt and ground eyelet. Then unbolt/remove the adjustment bolt at the top of the alternator.
Your alternator, with some maneuvering, will drop out the bottom of the engine bay.
Now the fun begins.
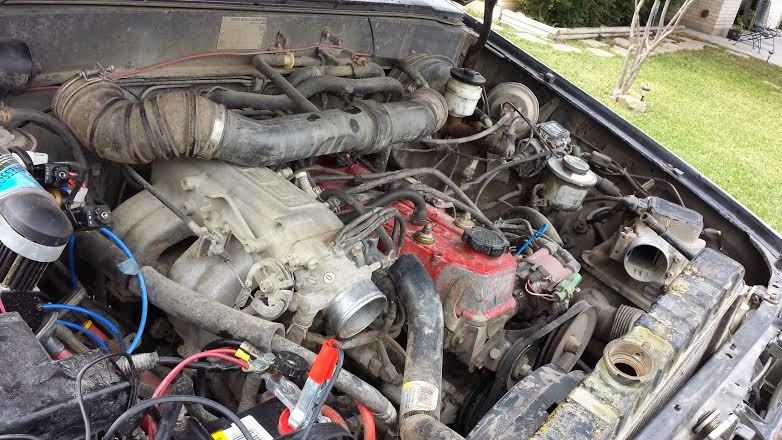 |
Removing coolant system |
To install the over-sized CS-144, you with need to create yourself some room. To do this, I removed my air intake hose, electric fan and my radiator. One screw at each end of the factory air intake, 4 corner bolts on the electric fan, and 4 corner bolts on the radiator, and the assemblies pulled out through the top of the engine bay.
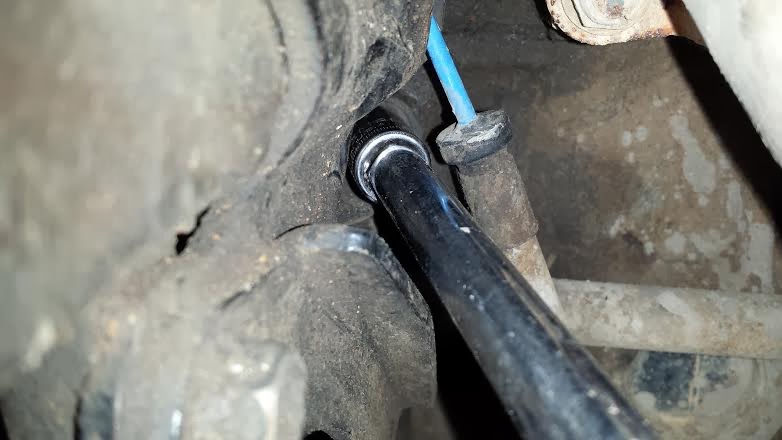 |
Upper factory Alt. bracket bolt |
To remove your factory alternator bracket, there will be 2 bolts on the top bracket, and 4 bolts on the lower bracket. The top bracket will have one bolt on the front of the engine block, between the power-steering belt tensioner and the power-steering pulley. The second bolt is near the dipstick tube, and partially behind the power-steering pump bracket. The surest way to reach this second bolt is to unbolt the power-steering bracket.
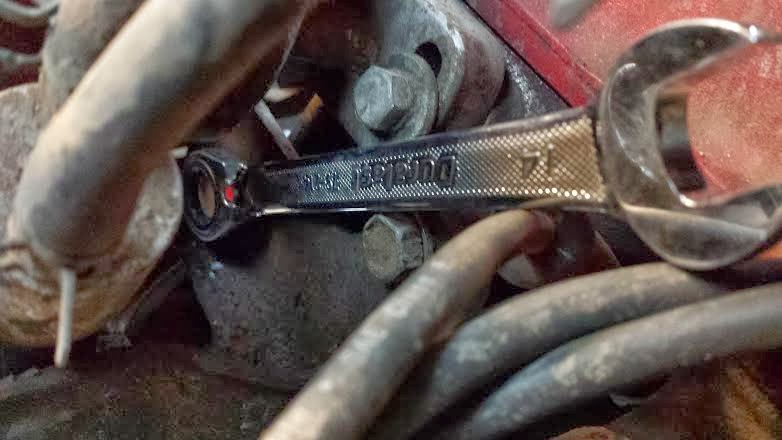 |
Hard-to-reach P.S. bracket bolt. |
If you have large hands, you will likely need to remove the distributor to reach this power-steering bracket bolt. Removing it is okay, but you need tiny hands to re-install it.
Once your 2 bolts have been removed, wiggle the bracket out of place and sell it on eBay. You won't need it where we're going.
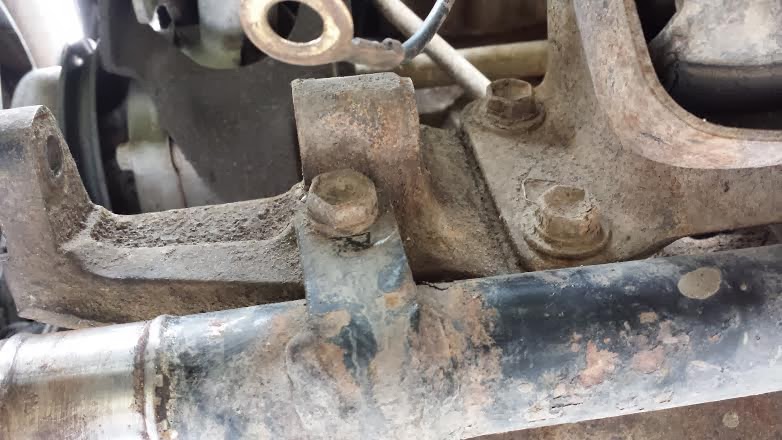 |
Lower Alt. bracket bolts (4) |
The lower alternator bracket has 4 bolts. Use a 2" drive extension and a breaker bar for the 2 engine mount bolts.
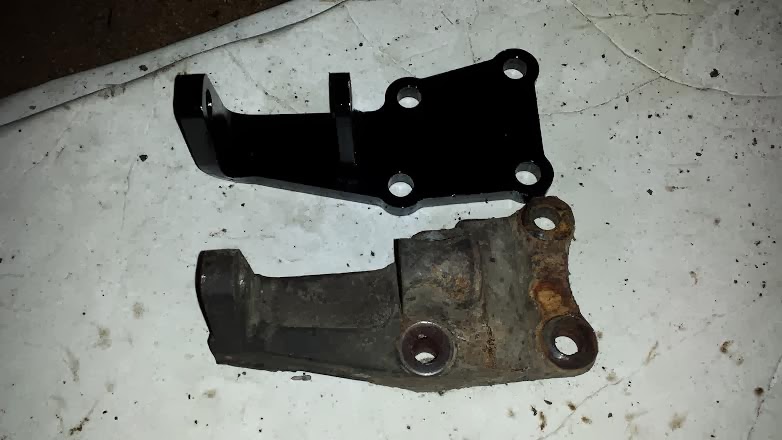 |
TrailGear relocation bracket
vs.
Factory alternator bracket |
When installing the new bracket, I installed the top-right bolt first, then love-tapped the bracket into place and installed the second engine mount bolt.
Now that your lower bracket is installed, install the CS-144 alternator and connect the ground cable to the swivel bolt.
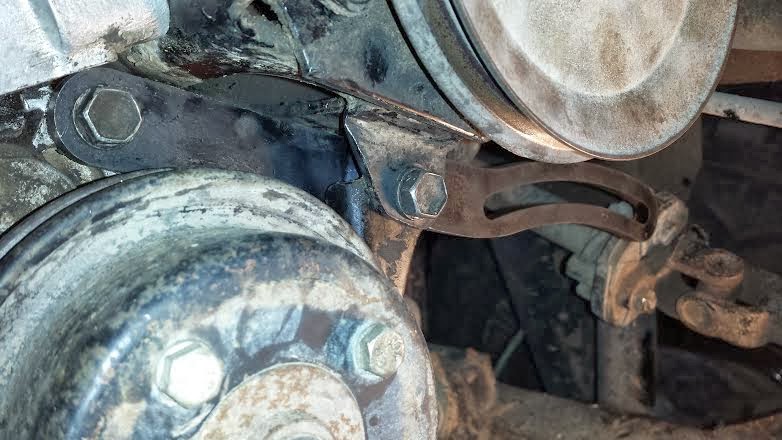 |
TrailGear relocation upper bracket |
After your CS-144 is bolted into place on the bottom, you can install the upper bracket. The upper bracket installs behind the power-steering pulley bolt (right), and bolts onto the block (left). My CS-144 isn't in the picture because I tried installing the whole bracket before installing the CS-144. This does not work because the CS-144 hits the upper bracket during installation and will not go into place.
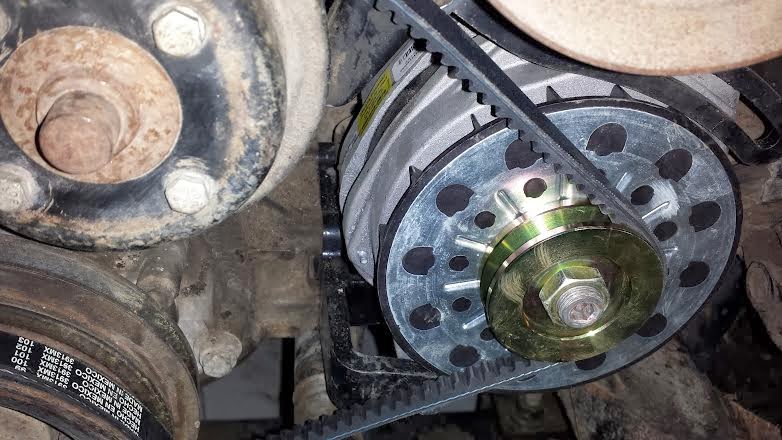 |
New alt. belt |
Now that your bracket is fully installed, you can install your new 1.5" longer belt and adjust the tension.
To move the CS-144 enough to install and tighten the belt, you will need to remove the radiator hose above the alternator. You can then slip the belt on and adjust like normal.
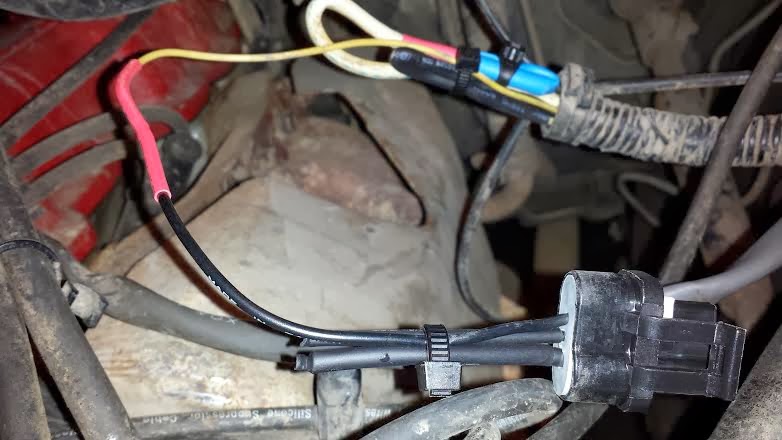 |
Factory wiring to GM plug |
Before you re-install the radiator hose, use that extra space to wire and install your GM plug. The plug comes in 3- and 4-wire options. Get the 3-wire.
Take your factory alternator harness, and cut off the factory alternator plug. Take your factory yellow wire ("L" or "Alt light") and connect it to the "L" on the GM plug.
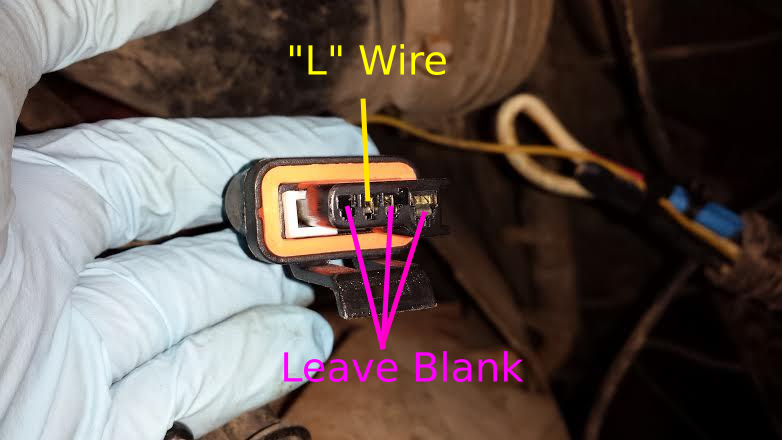 |
GM 3-wire plug |
The CS-144 should have a "P L I S" labeled on the alternator side of the plug, but in case yours doesn't, the GM "L" is the 2nd from the empty port.
You inadvertently just did the "one-wire mod."
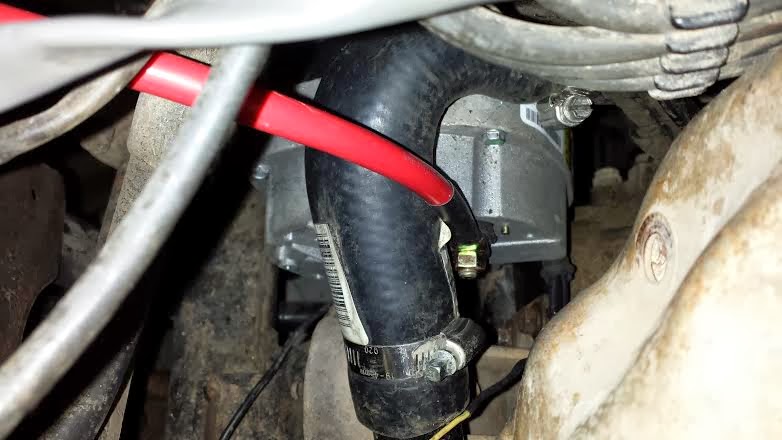 |
4-gauge hot with heat shrink at eyelet. |
Take your 78" 4-gauge and heat shrink over the extra exposed copper on the eyelet end. Coat eyelet with dielectric grease and install on CS-144. Then re-install the radiator hose.
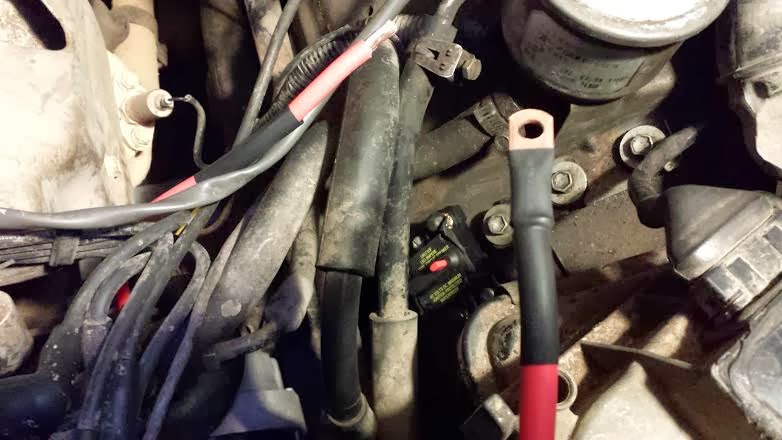 |
4-gauge, copper crimp-on connectors, and 150amp breaker |
At this point, run your 4-gauge to see where it'll fit best. I ran mine under the air box and over the radiator. Once you have your wire where you want it, you can see where you want to install your 150amp inline fuse/breaker.
Cut the 4-gauge (measure twice, cut once!) and install the crimp-on connectors. Heat-shrink over the extra copper and install with dielectric grease on to the inline fuse/breaker.
After your inline fuse/breaker is fully installed, tie the 4-gauge into your battery.
Side note: Keep an eye open for my future post, "Power Distribution Boxes: Tame the Main"
You are now ready to re-install your radiator, fan, and air intake.
You are finished installing your CS-144 alternator on your Toyota 22RE!
You will notice that you have some very small clearances between your steering and your CS-144. These have not caused a problem in my install, tensioning of the belt, or driving, but please keep an eye on your own install and make sure the steering is not contacting your CS-144.
Other Toyota-to-GM alternator upgrades